API St 603:2013 pdf free download.Corrosion-resistant, Bolted Bonnet Gate Valves—Flanged and Butt-welding Ends
5.3 Body Dimensions
5.3.1 Flanged Ends
5.3.1.1 Body end flanges shall comply with the dimensional requirements of ASME B16.5. Unless otherwise specified, raised face end flanges shall be provided. The Purchaser may specify a flange facing finish other than that specified in ASME B16.5.
5.3.1.2 Face-to-face dimensions shall be in accordance with ASME B16.10. Body end flanges and bonnet flanges shall be cast or forged integral with the body.
5.3.2 Butt-welding Ends 5.3.2.1 Butt-welding ends for valve sizes greater than DN 50 (NPS 2) shall conform to the requirements of ASME B16.25 and B16.34 for the bore specified for use without backing rings. Butt-welding ends for valves DN 50 (NPS 2) and smaller shall conform to the requirements of API 602. Conversion of a flanged end valve to a butt-welding valve for Class 300 and above may be permitted by agreement between the Purchaser and manufacturer.
5.3.2.2 End-to-end dimensions for butt-welding end class designated valves shall be in accordance with ASME B1 6.1 0, unless otherwise specified by the Purchaser.
5.3.2.3 Short pattern butt-welding end bolted bonnet valves are not permitted.
5.3.3 Body Seats
5.3.3.1 The inside diameter of the seat opening shall not be less than that specified in Table A-1 of Appendix A of ASME B16.34 for the applicable valve DN or NPS and pressure class.
5.3.3.2 Body seats may be separate or integral with the body. When hard facing is furnished, it shall be applied as a weld overlay of AWS A5.13 ECoCr-A or AWS A 5.21 ERCoCr-A, except as provided in 6.2.2, and shall have a minimum finished thickness of 1.6 mm (0.06 in.).
5.3.3.3 Where separate seat rings are provided, they shall be shoulder or bottom seated, and either threaded or seal welded in place, except that for DN ≤ 50 (NPS ≤ 2) rolled or pressed in seat rings may be used. Threaded seat rings may also be seal welded and shall be provided with lugs or slots to facilitate removal. The material used for seal welding shall provide for the same corrosion resistance as the valve body material.
5.3.3.3.1 Welding on seat rings and valves including any associated PWHT shall be performed using qualified welders and established procedures in accordance with ASME Section IX and the principles of Part D of ASME Section II, Appendix A.
5.3.3.4 Body seat rings shall have adequate seating area surface and shall have edges equipped with a radius or chamfer as necessary, to prevent galling or any other damage to the gate when the valve is operated against pressure.
5.3.3.5 Sealing compounds or greases shall not be used when assembling seat rings; however, a light lubricant having a viscosity no greater than kerosene may be used to prevent galling of mating threaded surfaces.
5.4 Bonnet Dimensions
5.4.1 When designing the stem, gland, lantern or spacer ring (if supplied) and backseat the manufacturer shall consider stem guiding and the prevention of packing extrusion.
5.4.2 A machined conical or spherical backseat shall be provided in the bonnet to contact a corresponding seating surface on the valve stem. The backseat shall be either an integral surface or weld-deposited hard facing with a minimum finished thickness of 1.6 mm (0.06 in.). Weld deposited hard facing is permissible as noted in 5.3.3.2 and as agreed upon by Purchaser.
5.4.3 Bonnets shall be one-piece castings or forgings.The gland bolting shall not be anchored to the bonnet or yoke through a fillet welded attachment or stud welded pins. The anchor design shall not include slotted holes or brackets which do not retain gland bolting during repacking.
5.4.4 Tapped test openings shall be provided only if specified in the purchase order.
5.5 Bonnet-to-body Joint
5.5.1 The bonnet-to-body joint shall be a flange and gasket type and the gasket shall not extend beyond the inner edge of the bolt holes.
5.5.2 For Class 150 valves, the bonnet-to-body joint shall be one of the following types illustrated in Figure 7 of ASME B16.5.API St 603 pdf download.API St 603:2013 pdf free download
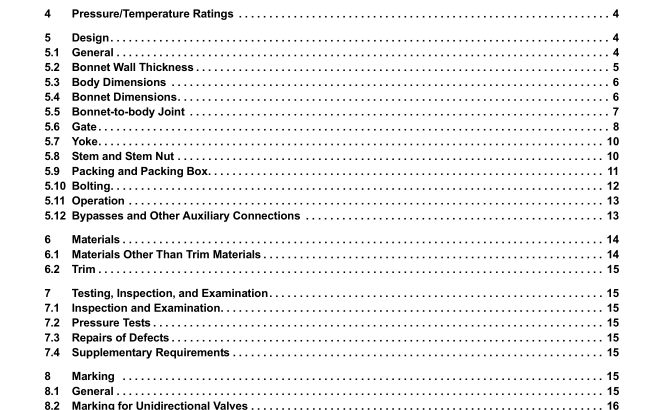