API RP 77:2018 pdf free download.Risk-based Approach for Managing Hydrocarbon Vapor Exposure during Tank Gauging, Sampling, and Maintenance of Onshore Production Facilities
4 Exposure and Risk Assessment
4.1 General Risk assessment is a common tool that is embraced by the industry and is applied throughout the life cycle of oil and gas operations. Risk assessment incorporates hazard assessment and exposure assessment, is conducted to identify and manage risk, and plays a key role in safety aspects of facility design as well as safe daily operation. However, this document does not provide a specific formula to the risk assessment process, but instead offers guidance in applying risk assessment principles, and provides hypothetical examples to help demonstrate how various risk assessment tools can be utilized (see Annex B examples). It is important to recognize that risk assessments help characterize the risk and provide information to risk managers to make decisions about actions that may, or may not, be needed to reduce risk.
4.2 Purpose of Exposure and Risk Assessment Oil field production tanks can present a variety of hazards. The combined makeup of these hazards and how they interact with one another for the particular tank and the state of operations at the time of the activity must be understood to effectively manage risk. The identified hazards (see Section 3) can be dynamic, so hazards should be assessed each time prior to undertaking tank gauging or sampling or conducting tank maintenance so that an accurate risk assessment can be performed, and appropriate risk management measures applied resulting in safe execution of the activity.
Exposure assessment is a key component of risk assessment. Exposure monitoring should be conducted as operations are initiated to establish a baseline assessment and determine the level of control required going forward. Data driven risk assessments take priority over other types of risk assessments specifically when the exposure data is reflective of the current conditions (no changes to process systems, worker tasks, etc.). Direct reading instruments and detector tubes can be utilized by operating personnel to confirm safe operational conditions and warn of unusual or changing conditions. Instruments should be selected and calibrated to cover the range of constituents (indicator compounds) monitored by the selected methods.
When performing a risk assessment, the assessor should focus on the hazards and exposure attributes that could occur under routine as well as non-routine conditions. Information such as the physical and chemical properties of the fluid, production volume, tank configuration, emission controls, and tasks performed should be available for assessment (see Section 3).
4.3 Risk Assessment and Life Cycle Phases
To conduct an exposure-based risk assessment, it is important to consider the life cycle of the well. The life cycle of an oil and gas well consists of many phases including: exploration, appraisal, design, development, production, and decommissioning. A variety of risks exists at each phase that can impact the potential for exposure to high concentrations of VOCs including hydrocarbons.
This section focuses on the activities and attributes of the design, development, and production phases that contribute or lead to changes in overall risk. During the design phase, compressors, separators, storage capacity, and other facility elements are sized and configured based on anticipated production rates and compositions. Some of the key considerations during the design phase have been identified in the Facilities Design Checklist in Annex A. For example, reservoir liquid/gas composition data and modeled flash analyses information can be utilized to predict anticipated vapor volumes at expected production rates to appropriately size separators and storage vessels, and to determine process safety and vapor emissions controls such as flaring systems.
The ability to isolate tanks is also an important consideration during this phase, since tanks that share vapor headspace connections can increase the volume of vapor available for release when a sampling or gauging hatch is opened. Additionally, the ability to isolate tanks to be gauged from tanks that are actively being filled can reduce vapors released from open hatches. Where vapor release is expected, mitigation options such as automatic or remote tank sampling and gauging systems can be considered, and are described in more detail in Section 6. During development phase activities such as flowback, the overall volume and composition of produced gases and liquids will vary, necessitating increased hazard and exposure assessments.API RP 77 pdf download.API RP 77:2018 pdf free download
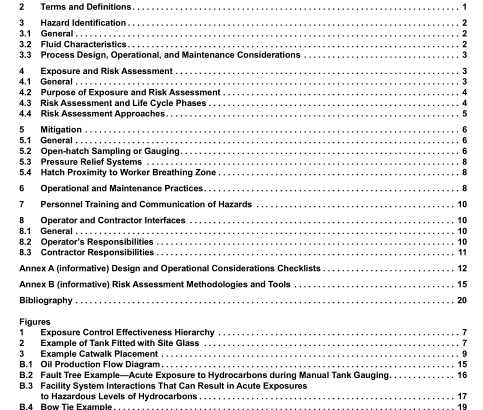