API RP 578:2018 pdf free download.Guidelines for a Material Verification Program (MVP) for New and Existing Assets
4 Considerations and General Concerns
4.1 Carbon Steel Substitutions in Low-alloy Steel Systems When considering the likelihood of material nonconformances, it is worth noting that, historically, the greatest number of material nonconformances with serious consequences have involved placing unapproved carbon steel components into low-alloy steel (e.g. 1 ¼Cr-½Mo, 2¼Cr-1 Mo, 5Cr-½Mo, 9Cr-1 Mo) piping systems.
4.2 Alloy Substitutions for Carbon Steel When determining the need to perform material verification on carbon steel, the owner/user should evaluate the effect that the process stream could have on substituted materials. In some cases, the substitution of hardenable alloy materials for carbon steel has resulted in failure and loss of containment. Examples of such systems include those handling wet hydrogen sulfide (H 2 S), hydrofluoric acid (HF), or sulfuric acid (H 2 SO 4 ). Where material substitution could lead to failure and/or loss of containment, the extent of verification should be planned and/or increased in order to foster effectiveness, as well as validate the materials specified for use.
4.3 Stainless Steel and Nonferrous Substitutions Within High-alloy Systems There is an assortment of stainless steels with varying compositions and varying corrosion resistances to different process streams. PMI should be considered by the owner/user depending upon the level of risk (probability and consequence of failure) based upon the potential damage mechanisms and damage rates associated with the installation of an unapproved high alloy during fabrication and installation. Examples of these situations include the substitution of stainless steels for Alloy 400 in HF Alkylation services, the substitution of a nonstabilized grade of stainless steel for a stabilized grade in a high-temperature service, or substitution of Type 304 SS for Type 31 6 SS where the molybdenum content is important for corrosion resistance.
4.4 Residual Elements in Carbon Steels in Hydrofluoric Acid Alkylation Units Carbon steels in some specific locations in HF acid service can experience increased corrosion rates based on the residual element (RE) content in the steels; e.g. Cr, Ni, Cu (refer to API RP 751 ). PMI methods can be used to assess the suitability of materials for HF service. Consideration should be given to the ability and/or accuracy of the PMI method to detect the various elemental concentrations, which are miniscule in comparison to the bulk analysis.
4.5 Process Units Susceptible to Sulfidation Carbon steels with low silicon (Si < 0.1 0%) content can corrode at a greater rate than carbon steels with higher silicon (Si > 0.1 0%) content when exposed to hydrogen‐free sulfidation conditions. These phenomena are discussed more extensively in API RP 571 and API RP 939-C. Owner/users with assets at risk from this type of degradation should consider the risks and the requirements needed to apply PMI material control in order to verify silicon levels and the effect on predicted corrosion rate. Alternatively, the owner/user may want to consider locating and conducting thickness measurements on all potentially susceptible carbon steel materials in a circuit exposed to hot sulfidation in order to determine if low-silicon components originally installed may be resulting in higher corrosion rates than the rest of a piping circuit.
4.6 Gasket Materials Gaskets in incompatible service may result in premature failures. The principles outlined in this document can be applied to gasket materials. The owner/user should define the material control methods to be used. The actual test procedures may be complex due to the construction of the gasket.
4.7 Refractory Installation Systems (Anchors) Testing to verify that the refractory anchors match specifications should be considered by the owner/user. Material specifications and maximum design temperatures for selected materials are discussed in API Std 560.
5 Material Verification Programs
5.1 General The owner/user shall establish a written material verification program indicating the extent and type of PMI to be conducted during the construction of new assets, retroactively on existing assets, and during the maintenance, repair, or alteration of existing assets.
For higher-risk systems, the owner/user should consider the need for employing a higher extent of in-process and final examination (up to 1 00 %) rather than random sampling, which may be more appropriate for lower- risk systems. The owner/user should also consider the need to conduct examinations after fabrication is complete at the point-of installation, to provide assurance that inadvertent substitutions did not occur.API RP 578 pdf download.API RP 578:2018 pdf free download
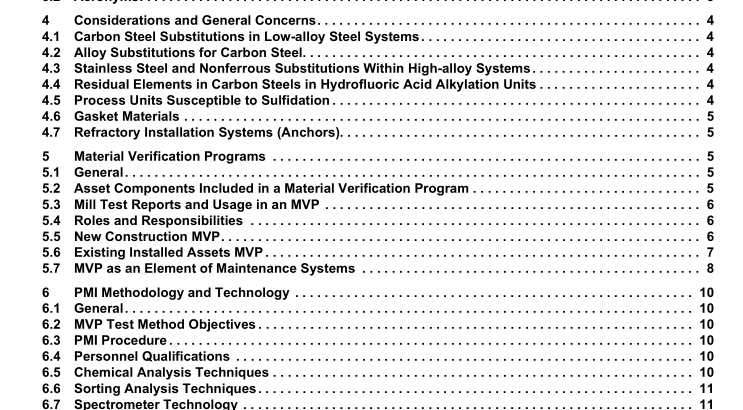