API MPMS 8.6:2020 pdf free download.Manual of Petroleum Measurement Standards Chapter 8.6 Refrigerated Light Hydrocarbon Fluids—Sampling of Liquified Natural Gas—Continuous and Intermittent Methods
5 Precautions
5.1 Precautions to be Taken in Handling LNG Because LNG has a very low boiling point, contact of the skin with LNG can cause frostbite and, if the gas diffuses into the air, it will lower the oxygen content, which can result in suffocation or, if ignited, fire. Suitable precautions shall be taken against these risks.
5.2 Partial Evaporation of the LNG Sample LNG normally exists in a state close to its boiling point. Therefore, partial evaporation readily occurs in the LNG transfer line and sampling line with minute heat input or by pressure variation. For this reason, extreme precautions shall be taken so that the collected gas sample represents transferred LNG with best possible accuracy.
5.3 Supervision During Sampling Pressures, temperatures, and flow rates in the LNG transfer line and the sampling system shall be monitored continuously. Frequent inspection of the entire system shall be made, paying particular attention to any leak or failure of the thermal insulation. Defects identified by such inspections shall be remedied immediately.
6 Apparatus
6.1 Materials Used The materials of construction of the sampling system shall have sufficient strength and durability to withstand the pressure and temperature conditions to which they are exposed. The possibility of embrittlement of materials at low temperatures shall be taken into account. Materials shall neither be affected by exposure to the fluids handled nor have any effect on the composition of the fluids being sampled.
6.2 Sampling Extraction Point The sampling point is generally located
— on the main loading pipe (line) after the LNG pumps send-out;
— on the main unloading pipe (line) after the unloading arms. LNG should be sampled during a stable flow (refer to Figure 8). It is preferable to install the sampling point as close as possible to the custody transfer point (loading arm flange/ship manifold or main header) so that the characteristics of LNG do not change before it is transferred because of potential heat input. The influence of heat input is limited when the flow does not vary in the properly insulated main unloading/loading line.
LNG normally exists in a state close to its boiling point. Therefore, partial vaporization can occur in the LNG transfer line and the sampling line from the pipeline to the sampling system entry, with minute heat input or by pressure variation. Precautions shall be taken with the sample system design and handling of the samples so that the collected vaporized sample accurately represents the transferred LNG. All the extracted sample from the probe in the pipeline must enter the sample system and be completely vaporized. Each step of the sampling process shall be taken without allowing the integrity of the sample composition to be compromised. The LNG sub-cooled condition can be determined by using the method proposed in ISO 8943 (Annex A).
6.3 Sample Probe Sample probes shall be located at points in the pipeline where the LNG is in a sub-cooled condition.
The degree of sub-cooling at a sampling point shall be ascertained by observation of the temperature and pressure of the LNG at that point and comparing the temperature with the boiling point of the LNG at the same pressure as calculated from the composition of the LNG (see Annex A). In the case of multiple transfer lines, the sample probe shall be located downstream of the manifold, if one exists. Otherwise, each line shall be provided with a sampling point. Where multiple lines are provided with individual sampling points and the flow rates in the respective lines differ, the flow rate in each line shall be measured and the sample flows made proportional to these rates of each line separately.API MPMS 8.6 pdf download.API MPMS 8.6:2020 pdf free download
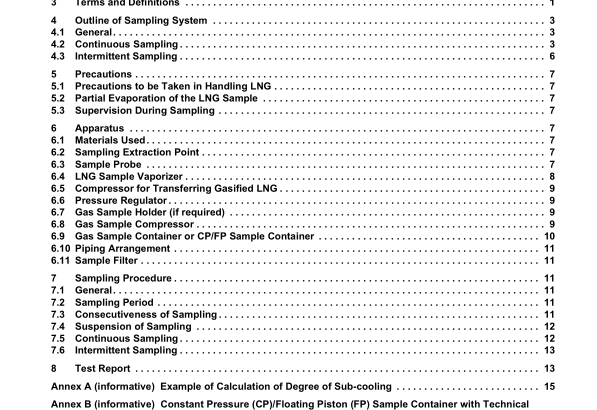