API RP 934-E:2010 pdf free download.Recommended Practice for Materials and Fabrication of 1 1 / 4 CR- 1 / 2 Mo Steel Pressure Vessels for Service Above 825 °F (440 °C)
NOTE The J-factor is not applicable to these alloys, and an X-bar limit has been adopted as a means of restricting the concentration of elements that contribute to reheat cracking of the steel. The chemistry restrictions described above along with other aspects of this RP are designed to provide the steel with resistance to the reheat cracking phenomenon described in API 938-A.
5.4 Heat Treatment All product forms shall be annealed, normalized and tempered (N&T) or quenched and tempered (Q&T) to meet the required mechanical properties. For thickness > 2 in. (50 mm), Q&T may be required to meet fracture toughness specifications for the steel. Annealed steel and lower Class levels should be specified for applications involving high temperature service where the primary failure mechanism is creep rupture. For equipment exposed to cyclic service and where fatigue is an important factor the use of N&T or Q&T heat treatment and higher class levels may be more appropriate.
5.5 Mechanical Properties
5.5.1 Location of Test Specimens Test specimens for establishing the tensile and impact properties shall be removed from the following locations:
a) Plate—From each mother-plate with the same heat treatment, transverse to the rolling direction in accordance with SA-20 at the standard test locations and at the 1 / 2 T location. When permitted by the applicable product specification, coupons for all tests shall be obtained from the 1 / 2 T location only. If required, 1 / 2 T specimens shall be used for hot tensile tests.
NOTE If multiple plates are cut from one motherplate only one set of specimens from the motherplate is required. b) Forging—From each heat transverse to the major working direction in accordance with SA-182 or SA-336, and test specimens shall be taken at 1 / 2 T of the prolongation or of a separate test block. A separate test block, if used, shall be made from the same heat and shall receive substantially the same reduction and type of hot working as the production forgings that it represents and shall be of the same nominal thickness as the production forgings. The separate test forging shall be heat treated in the same furnace charge and under the same conditions as the production forgings. c) Pipe—From each heat and lot of pipe, transverse to the major working direction in accordance SA 530 except that test specimens shall be taken from 1 / 2 T.
5.5.2 Tensile Test Requirements
5.5.2.1 Tensile testing of plates and forging materials shall comply with the applicable code(s) and the following additional requirements.
5.5.2.2 Test coupon shall be heat treated to represent the maximum post-weld heat treatment per 3.1.6.
5.5.2.3 Tensile properties at room temperature shall meet the requirements of the applicable code(s).
5.5.3 Impact Testing Requirements Charpy V-notch (CVN) impact testing shall be performed for all 1 1 / 4 Cr- 1 / 2 Mo steel material used for pressure containing components except bolting. CVN impact tests shall comply with the applicable code(s) and the following additional requirements.
a) Test coupons from forgings shall be oriented transverse to the major direction of metal flow.
b) Test coupons heat treated to represent both the minimum and maximum post-weld heat treatments per 3.1.7 and 3.1.6 shall be tested and meet the following requirements. The minimum CVN impact values shall be 40 ft-lbs (54 Joules) average of three specimens at 0 °F (–18 °C) and 20 ft-lbs (27 Joules) minimum for a single specimen at 0 °F (–18 °C). In addition, if the MDMT is < 0 °F (–18 °C), Code requirements for impact testing must also be met. If the toughness levels at the MDMT of < 0 °F (< – 18 °C) meet the toughness criteria levels (40/20 ft-lbs) listed above, retesting at 0 °F (–18 °C) is not needed.API RP 934-E pdf download.API RP 934-E:2010 pdf free download
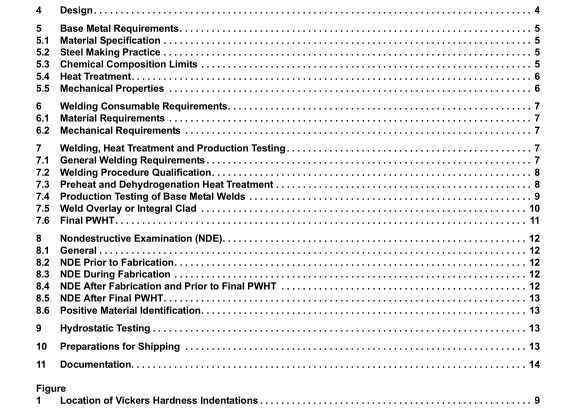