API RP 934-C:2008 pdf free download.Materials and Fabrication of 1 1 / 4 Cr- 1 / 2 Mo Steel Heavy Wall Pressure Vessels for High-pressure Hydrogen Service Operating at or Below 825 °F (441 °C)
6.1.3 Low hydrogen welding consumables, including fluxes, having a maximum of 8 ml of diffusible hydrogen for every 100 g of weld metal, H8 per AWS A4.3, should be used. They should be baked, stored, and used in accordance with manufacturer’s instructions (holding in electrode oven, length of time out of oven, etc).
6.2 Mechanical Requirements
6.2.1 Tensile Properties The tensile properties of the deposited weld metal should meet those of the base metal in accordance with 5.5.2.
6.2.2 Impact Properties Prior to the start of fabrication, each lot of electrodes, heat of filler wire, and combination of lot of flux and heat of wire, should be screened by impact testing of weld deposit in accordance with 5.5.3.
7 Welding, Heat Treatment, and Production Testing
7.1 General Welding Requirements
7.1.1 Base metal surfaces prior to welding or applying weld overlay should consist of clean metal, prepared by machining, grinding, or blast cleaning.
7.1.2 All welded joints including non-pressure attachments to the vessel body should: a) have full penetration joint design; b) be located so that full ultrasonic examination of welds can be made after fabrication and after installation is complete (in cases where this is not practical, the manufacturer should propose alternate NDE methods to verify weld quality), and; c) be made sufficiently smooth to facilitate NDE (MT, PT, UT, or RT), as applicable.
7.1.3 All welding should be completed prior to final PWHT except welding of internal attachments to the corrosion resistant weld overlay or cladding. For these attachment welds, a WPQT or mockup test should be performed to verify that this does not produce a HAZ in the base metal unless waived by the purchaser.
7.1.4 All weld repairs to base metal, weld joints and weld overlay should be performed using a repair welding procedure qualified in accordance with 7.2, and should meet all the same requirements as the normal fabrication welds.
7.2 Welding Procedure Qualification
7.2.1 Welding procedures should be qualified in accordance with ASME BPVC, Section IX, with the following additional requirements.
7.2.2 Base metal for welding procedure qualification tests should be made from the same ASME base metal specification (same P-number and Group number) and similar in chemistry as specified for the vessel, but either plate or forging may be used. The welding electrodes, wire and flux combination should be of the same type and brand as those to be used in production welding.
7.2.3 Two Vickers hardness traverses of the weld joint should be made on a weld sample in the minimum PWHT condition. These hardness traverses should be performed at 1 / 16 in. (1.5 mm) from the internal and external surfaces as shown in Figure 1. The HAZ readings should include locations as close as possible [approximately 8 mils (0.2 mm)] to the weld fusion line. Each traverse includes ten hardness readings for a total of 20 hardness readings per weld sample. The hardness should not exceed 235 HV10.
7.2.4 A tensile test, transverse to the weld, should be performed on a weld joint of the heat treated test plate in the maximum PWHT condition and should meet the ambient temperature properties specified for the base metal in 5.5.2.
7.2.5 Charpy V-notch impact testing should be performed on weld metal and HAZ of the heat-treated test plate in the minimum and maximum PWHT conditions. These impact tests should be performed for each welding procedure and should meet the impact test temperature and acceptance requirements in 5.5.3.
7.2.6 All WPSs and PQRs should be approved by purchaser prior to fabrication.
7.3 Preheat and Dehydrogenation Heat Treatment (DHT)
7.3.1 Preheat All base metals should be heated to a minimum of 300 °F (150 °C) during all welding, rolling, thermal cutting, and gouging operations (except during weld overlay, see 7.5.4). For butt welding and attachment welding, this preheat temperature should be maintained through the entire plate thickness for a distance of at least one plate thickness on either side of the weld but need not extend more than 4 in. (100 mm) in any direction from the edge of the weld. The preheat temperature should be maintained until PWHT or DHT is performed in accordance with 7.3.2.
7.3.2 Dehydrogenation Heat Treatment (DHT) The DHT should be performed at a minimum metal temperature of 570 °F (300 °C) for duration of one hour minimum.API RP 934-C pdf download.API RP 934-C:2008 pdf free download
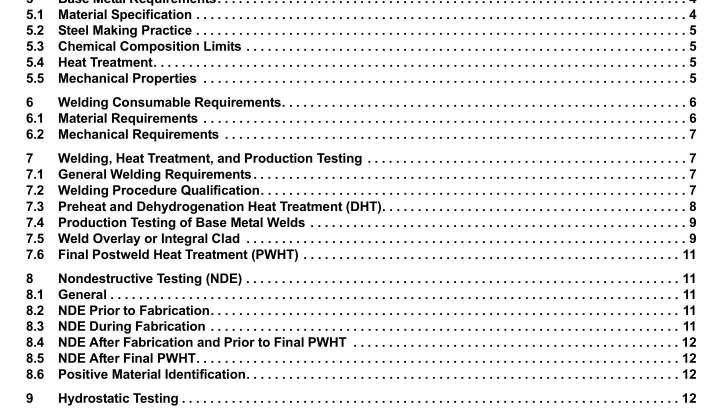