API RP 615:2010 pdf free download.Valve Selection Guide
4.2 Valve Types
Consideration of valve types:
— gate valves (API 600, API 602, API 603),
— ball valves (API 608),
— plug valves (API 599),
— butterfly valves (API 609),
— check valves (API 594, API 602),
— globe valves (API 602).
4.3 Other Considerations
Other considerations to take into account:
— pressure class and size;
— fluid service;
— materials of construction;
— valve trim selection;
— valve special features such as fire testing, cavity venting, purge connections, etc.;
— flow capacity and pressure loss.
5 Primary Valve Types
NOTE Some valve types are capable of performing multiple functions. If not used for their primary intended function, they may not perform well or may experience a premature failure.
5.1 Valves to Stop Flow or to Provide for Equipment Isolation (Block Valves)
5.1.1 Gate Valves
5.1.1.1 General The gate valve is a common type of block valve for on-off service. The gate valve’s closure member (gate) moves out of the flow stream perpendicular to the flow path. Typical process gate valves use a wedge type gate. Upon closing the gate to effect shutoff, the two faces of the gate engage the matching angle of the valve body seats. Turning the handwheel forces the disc firmly into the seats which, assisted by line pressure, provides for shutoff of flow. The API standards covering gate valves are: API 600, API 602, and, API 603. Gate valves are typically not recommended for throttling service.
5.1.1.2 API 600 Gate Valves API 600 on gate valves covers sizes from NPS 1 up to NPS 24 in pressure classes from Class 150 to Class 2500 with flanged or butt-welding ends. This standard was developed for refinery applications to provide a robust, heavy wall design suitable for service up to 538 °C (1000 °F). Pressure-temperature ratings for these valves are given in ASME B16.34 (standard class) for the listed materials. Body and bonnet wall thickness specified in API 600 are greater than those in ASME B16.34 thereby providing for an additional corrosion allowance capability. Stem diameters are also specified. The standard gate in API 600 is one-piece, wedge-shaped, either solid or flexible wedge. The “flexible” wedge design provides for a small amount of angular deflection of the disc faces to provide for a better engagement with the body seats. This allows the wedge to accommodate some deviation from the ideal seat position caused by deflection of the valve body due to line stresses or thermal expansion, thereby resulting in improved seat tightness and reduced potential for gate binding in the closed position. See Figure A.1 for a typical API 600 gate valve.
5.1.1.3 API 602 Gate Valves API 602 covers the smaller size gate valves in sizes up to NPS 4 for pressure classes from Class 150 to Class 1500 including the special Class 800. API 602 gate valves are commonly used in process plants in sizes from NPS 1 / 2 to NPS 2 in Class 800 with threaded or socket-welding ends. The standard port size is smaller than the line size but full port is an available option. These small valves are usually made from forgings. Flanged-end and butt-weld end valves are available where use of socket weld or threaded ends may not be desired, for example, in compressor lube oil service. See Figures A.2 and A.3 for typical examples of API 602 gate valves.
5.1.1.4 API 603 Gate Valves API 603 was developed to provide a lower cost alternative to API 600 valves in corrosive, lower pressure services. They provide a lighter-weight, corrosion-resistant design made of a stainless or nickel alloy with a thinner body wall than API 600 valves. API 603 specifies wall thicknesses comparable to those in ASME B16.34. Like API 600, API 603 specifies minimum stem diameters. These valves are available in flanged or butt-weld ends in pressure classes 150, 300, and 600 and in sizes NPS 1 / 2 through NPS 24. The wedge design is typically solid or flexible although split wedge and parallel-sided double disc gates are covered in the standard. Hardfacing may be specified to reduce galling tendency of stainless wedge seat faces to stainless body seat faces. See Figure A.4 for an example of a gate valve from API 603.
5.1.1.5 Pressure seal Bonnet Gate Valves Gate valves with a special “pressure seal” bonnet closure design that avoids bonnet flanges are available from several manufacturers for Class 600 and higher and may typically be used in hydrogen service. The pressure seal bonnet design uses a compact body-bonnet joint that is pressure-assisted so that with increasing pressure the bonnet seals more tightly. The use of this design should be restricted to services that are not highly corrosive to avoid damage to the pressure seal element. Maintenance that involves reassembly of the pressure seal should be done with the help of a manufacturer’s representative or a qualified valve repair organization to ensure proper assembly, testing, and preloading of the seal ring. Replacement seal rings may be available only from the original manufacturer. These valves are often supplied with weld ends thereby eliminating heavy line flanges. This valve design is not covered in API 600.API RP 615 pdf download.API RP 615:2010 pdf free download
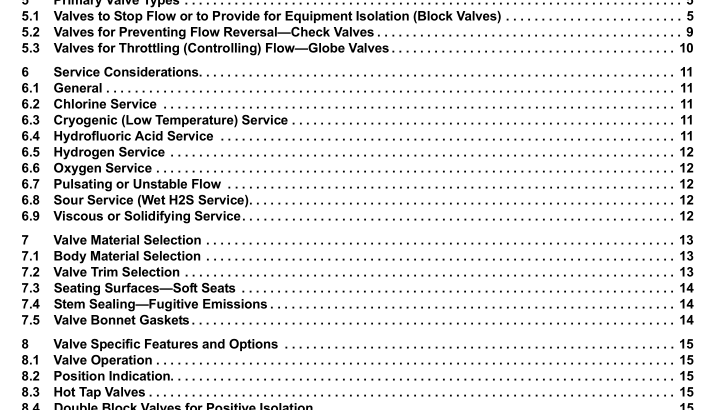