API RP 5C6:2006 pdf free download.Welding Connections to Pipe
7.5 POSTWELD HEAT TREATMENT When required, PWHT shall be in accordance with the applicable qualified WPS or written procedure.
7.6 WELDING CONTROLS
7.6.1 The fabricator’s welding control system shall include procedures for monitoring, updating, and controlling the qualifica- tion of welders or welding operators and the use of WPS.
7.6.2 Instruments to verify temperature, voltage, and amperage shall be serviced and calibrated in accordance with written pro- cedures or specifications. Temperature indicating crayons may be used to monitor preheat and interpass temperature.
8 Inspection
8.1 CALIBRATION OF MEASURING AND TEST EQUIPMENT Equipment used to inspect, test or examine material or other equipment shall be identified, controlled, calibrated, and adjusted at specified intervals in accordance with documented manufacturer instructions, and consistent with referenced industry standards, to maintain the accuracy required by this specification.
8.2 CONNECTOR SQUARENESS AND ALIGNMENT VERIFICATION Squareness of each connector welded to pipe shall be inspected to verify conformance with the following requirements.
8.2.1 Squareness Verification Squareness is a measurement of the connector with respect to the pipe axis and shall be inspected to assure compliance with the requirements set forth in this recommended practice.
a. The maximum allowable deviation from square shall be 1 / 16 inch per 12 inches.
b. All squareness measurements utilizing the pipe O.D. as a reference surface shall be taken at a distance of no less than 2 inches away from the weld. c. Squareness verification measurements shall be taken at 2 locations as a minimum at 90 degrees apart. 8.2.2 Alignment Verification When alignment verification is specified as a supplementary requirement (SR 34), the fabricator shall perform alignment verifica- tion as specified below. Connector to pipe alignment verification is a measurement of one connector face relative to the connector face on the opposite end of the pipe. The measurement includes axial alignment and connector parallelism.
8.2.3 Equipment Typical alignment verification equipment consists of a set of two fixtures including a target and a telescope (or other sighting or image projection device). These fixtures are positioned on opposite ends of the joint being verified such that they are both parallel with the connector or pipe face and centered with the axial centerline of the connector or pipe end. The target typically consists of a well defined center area (bull’s eye) with concentric target circles of a known diameter. The sighting device should be of suffi- cient magnification to observe sight placement within the prescribed target circle for the length of joint being fabricated (usually 40 feet).
8.2.4 Alignment method With alignment fixtures made up to the connectors (or pipe end), the connectors should be manipulated and tack welded to satisfy the alignment acceptance criteria specified in SR 34.
8.3 NONDESTRUCTIVE EXAMINATION OF WELDMENTS Conduct visual examination in accordance with API Standard 1104 with the following additional requirements.
8.3.1 Weld Reinforcement Visual inspection shall be conducted to verify compliance with the following restrictions to both the internal and external weld reinforcements. At no point shall the crown of the weld be below the surface of the pipe nor shall it be raised above the parent metal by more than 1/16 inch. Those welds where the raised height of the weld reinforcement exceeds the limits set forth may be brought to within tolerance by grinding. Weld reinforcement may exceed 1/16 inch when welding reduced bore connectors, girth weld on end opposite the elevator lift end, and other special cases. The fabricator and purchaser may need to consider drift and handling equipment requirements to ensure compatibility.
8.3.2 Radiographic Examination Radiographic examinations shall be conducted in accordance with the procedures set forth in API Standard 1104, Sections 8.1.1 through 8.1.13. All discontinuities located by radiographic examination shall be subject to the acceptance standards presented in Section 6 of API Standard 1104.
8.3.3 Production Weld Test Frequency Nondestructive testing consisting of radiographic and visual inspection shall be conducted on 100 percent of all production welds.API RP 5C6 pdf download.API RP 5C6:2006 pdf free download
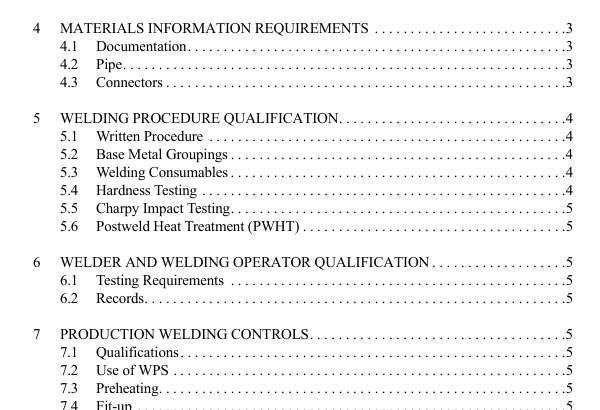