API RP 13M-2004 pdf free download.Recommended Practice for the Measurement of Viscous Properties of Completion Fluids ANSI/API Recommended Practice 13M First Edition, July 2004 Identical to ISO 13503-1: 2003 ISO 13503-1 Petroleum and natural gas industries— Completion fluids and materials— Part 1: Measurement of viscous properties of completion fluids
8.2.2.1.2 Operation
8.2.2.1.2.1 Preparation Rotor and bob shall be properly aligned. All parts in contact with the fluid shall be at the same temperature as the fluid. Use of the standard cup provided by the manufacturer is recommended. Other vessels may be used, however the vertical space between the bottom of the bob and bottom of the vessel shall be at least 13 mm (0,50 in).
8.2.2.1.2.2 Procedure The non-crosslinked fluid sample to be tested shall be representative of the fluid as a whole, and air entrainment shall be minimal. After being placed in the viscometer, the fluid is stirred for 10 s to 15 s at the highest shear rate for which a measurement is to be made. Viscosity measurements should be made from lowest to the highest shear rate. Record the average reading 20 s after reading is stabilized at each shear rate.
8.2.2.1.3 Calculations In order to convert a reading in revolutions per minute to shear rate, use the following formula: 1 r/min = 1,704 s −1 Viscometric calculations shall be performed according to the manufacturer’s specified procedure. For rheological calculations, see Clause 9.
8.2.2.2 Pressurized concentric-cylinder viscometer 2) , to measure the viscous and rheological properties of completion fluids at elevated temperatures. Pressurization minimizes the effect of entrained air on measured parameters and allows measurements to be made at temperatures above the atmospheric boiling point of the sample. Multiple-point measurements may be suitable for determining the rheological parameters of fluids. Any pressurized concentric-cylinder viscometer with the dimensions shown in Figure 3 may be used.
8.2.2.2.1 Calibration Measure the temperature of the fluid being tested according to the manufacturer’s specified procedure which shall be traceable to a national/international standard such as ISO, ASTM, DIN, or equivalent. Measure the rotor or sleeve speed according to the manufacturer’s specified tachometer calibration procedure which shall be traceable to a national/international standard such as ISO, ASTM, DIN, or equivalent. Use one of the following calibration methods: a) preferred method Verify system using a standardized Newtonian calibration fluid traceable to a national/international standard such as ISO, ASTM, DIN or equivalent. A calibration oil viscosity shall be selected to encompass the shear rate/shear stress envelope to be evaluated. The calibration shall be conducted at ambient pressure. NOTE While the compressibility of aqueous fluids are not significantly affected by the pressure, some calibration oils, in particular silicone oils, are affected by pressure.
b) alternative torque-only calibration Measure according to the manufacturer’s specified calibration procedure (e.g. hanging weight), which shall be traceable to a national/international standard such as ISO, ASTM, DIN, or equivalent.
8.2.2.2.2 Operation 8.2.2.2.2.1 Instrument preparation Pre-heat thermal bath (if equipped) to test temperature. All temperatures in this document refer to actual temperature of the fluid. 8.2.2.2.2.2 Procedure The following procedures shall be followed.
a) Loading, pressurizing and heating the fluid Load the fluid to be evaluated into the viscometer immediately after the last component is added according to mixing procedure. Place 52 cm 3 of fluid in the viscometer. This volume is sufficient to fully cover the bob. Pressurize the system with nitrogen to a minimum of 2,75 MPa (400 psi) and immediately start shearing at 100 s −1 . When shearing of the fluid starts, define the elapsed time as zero (t = 0) and begin heating the fluid. All actions in this paragraph shall be completed within 45 s. Optionally, for an ambient-temperature shear ramp [described in 8.2.2.2.2 b)], elapsed time is defined as zero (t = 0) immediately after completing this ramp, and fluid heating is begun. At 20 min elapsed time, the fluid temperature shall be no lower than 5 % below (base = 0 °C) and no higher than 3 °C (+ 5 °F) above the desired test temperature. In addition, at 30 min elapsed time, and for the remainder of the test, the fluid temperature shall be within ± 3 °C (± 5 °F) of the test temperature.API RP 13M pdf download.API RP 13M:2004 pdf free download
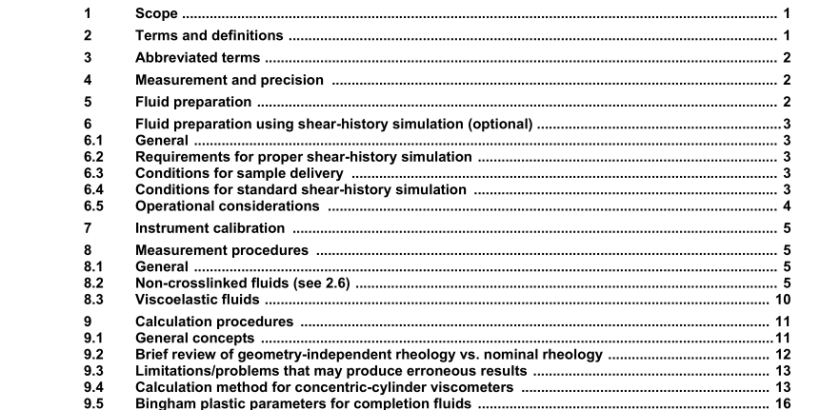