API STD 603:2013 pdf free download.Corrosion-resistant, Bolted Bonnet Gate Valves—Flanged and Butt-welding Ends
5.7 Yoke 5.7.1 The yoke may be either an integral part of the bonnet or a separate part.
5.7.2 Yokes that are separate shall have yoke-to-bonnet mating surfaces machined so as to assure a proper bearing assembly interface. Separate yokes shall be bolted to the bonnet with through bolts.
5.7.3 The yoke-to-stem nut bearing surfaces shall be machined flat and parallel. A lubricating fitting shall be provided for the bearing surfaces.
5.8 Stem and Stem Nut
5.8.1 The minimum stem diameter measured at the section that passes through the packing, shall be in accordance with Table 1. The actual stem diameter shall take into account the valve design details and the stem materials strength characteristics. The stem surface area in contact with the packing shall have a surface finish, Ra, of 0.80 µm (32 µin.) or smoother.
NOTE The stem strength should be considered when calculating the maximum input force from the handwheel and gearbox (if equipped) in accordance with MSS SP-91 or in accordance with maximum rim pull when specified by the Purchaser.
5.8.2 Stems shall have a gate attachment means at one end and an external trapezoidal style thread form at the other. Stem nuts shall be used for handwheel attachment and to drive the operating stem thread.
5.8.3 The stem-to-stem nut threads shall be of trapezoidal form as specified in ASME B1.5 or ASME B1.8, (minor modifications are permitted for either thread) with nominal dimensional variations allowed. The thread major diameter may be less by a maximum of 1.6 mm (0.06 in.) than the diameter of the stem that passes through the packing. Stem threads shall be left-handed so that a direct operated handwheel rotated in a clockwise direction closes the valve.
5.8.4 The stem shall be one-piece wrought material. A stem that is a welded fabrication or threaded assembly shall not be provided. 5.8.5 Out of straightness of the entire length of the stem shall not exceed 0.001 mm/mm (0.001 in./in.) 5.8.6 The stem end that connects to a gate shall be in the form of a “T,” except that for a double-disc gate, the end connection may be threaded. 5.8.7 The stem connection shall be designed to prevent the stem from turning or from becoming disengaged from the gate while the valve is in service.
5.8.8 The stem design shall be such that the strength of the stem to gate connection and the part of the stem within the valve pressure boundary shall, under axial load, exceed the strength of the stem at the root of the operating thread.
5.8.9 The one-piece stem shall include a conical or spherical raised surface that seats against the bonnet backseat when the gate is at its full open position.
NOTE The existence of a stem-bonnet backseat, is not meant to imply a manufacturer’s recommendation of its use for the purpose of adding or replacing packing while the valve is under pressure.
5.8.10 The yoke shall retain the stem nut which links the handwheel to the stem. For valves larger than DN 150 (NPS 6) Class 150, DN 100 (NPS 4) Class 300 or DN 50 (NPS 2) Class 600, the stem nut arrangement shall be designed to: a) Permit the removal of the handwheel, without allowing the stem and gate to drop into the closed position, if the handwheel is removed when the valve is in the open position.
b) Allow the stem nut to be replaced, with the stem secured, without affecting the pressure retaining capability of the bonnet assembly. However, replacement under pressure is not recommended.
5.8.11 The stem-nut-to-handwheel attachment shall be through a hexagonal interface, a round interface having a keyway or another means of equivalent strength. Valves shall have a stem operated by a rotating stem nut mounted at the top of the yoke. The stem nut shall have a hexagonal shank, a round shank with a keyway, or another drive of equivalent strength and durability for attachment to the handwheel. API STD 603 pdf download.API STD 603:2013 pdf free download
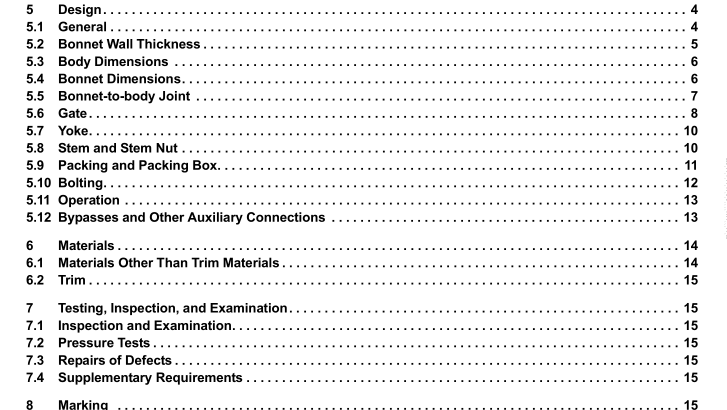