API Spec 20B:2013 pdf free download.Open Die Shaped Forgings for Use in the Petroleum and Natural Gas Industry
4.4.1 FSL-1 A change in material group as shown in Table 2 from the forging that was previously qualified requires requalification of the forging.
4.4.2 FSL-2
4.4.2.1 Qualification requirements specified for FSL-1 are required for FSL-2.
4.4.2.2 A change to the forging practice resulting in a lower hot work ratio than that used to produce the qualification forging requires a requalification.
4.4.2.3 Any change in the melt practice used to qualify the forging requires a requalification.
4.4.2.4 A change in the as-forged weight range class as shown in Table 1 from the forging that was previously qualified requires requalification of the forging.
4.4.2.5 A change from press or hammer equipment to a ring rolling process.
4.4.3 FSL-3 4.4.3.1 Qualification requirements specified for FSL-1 and FSL-2 are required for FSL-3.
4.4.3.2 An increase in the minimum specified yield strength or minimum specified tensile strength in accordance with the applicable design standard above the values qualified for a given material subgroup requires a requalification.
4.4.3.3 A change in the basic type of forge equipment used (mechanical, press, hammer, ring roller, etc.) from the forging that was previously qualified requires requalification of the forging.
4.4.3.4 Any change of the subgroup in material groups 1, 2, 3, 4, and 5 from Table 2 requires a requalification.
4.4.4 FSL-4 4.4.4.1 Qualification requirements specified for FSL-1, FSL-2, and FSL-3 are required for FSL-4.
4.4.4.2 A change in the actual melt source used to supply the starting material from the forging that was previously qualified requires requalification of the forging.
4.4.4.3 A change in specific material grade within a subgroup requires requalification of the forging (Ex. 4130 and 4140 require separate qualifications).
4.4.4.4 A change in the immediate postforge thermal process used from the forging that was previously qualified requires requalification of the forging.
4.5 Records of Qualification The following records are required to document the qualification of the forging. a) Starting material, grade, UNS number, where applicable, heat number, material specification, supplier name, supplier mill, size, hot work ratio, cut weight, melt practice and ladle refinements, cleanliness, actual chemistry, minimum/maximum element tolerance, incoming material inspection/evaluation method, MPS revision level, and qualification number.
b) Forging parameters: hot work temperature range, description of each forging operation including product configuration at start and finish of each operation, and hot work ratio for each step, forge equipment used. c) Post forging parameters: time, temperature, and media of cooling/bake-out, heat treatment specification and actual times and temperatures, cooling media, heat treatment equipment used. d) Test records: records of the examination, mechanical testing, and metallographic evaluations as described in Section 4.
5 Production Forgings
5.1 Qualification of Procurement Sources for Starting Material
5.1.1 Only melt source facilities that are approved by the forging supplier shall be used to supply starting material such as billet or ingot material. The forging supplier shall have a documented procedure, fully implemented, for qualifying starting material suppliers for each specific size and grade of starting material. The approval process shall be based on both a quality assurance and a technical evaluation. The approval process shall establish the methodology by which the starting material supplier will be evaluated on an ongoing basis to maintain their status as an approved supplier. 5.1.2 The maintenance of an acceptable quality program, such as an ISO registration, is not sufficient by itself to satisfy the requirements of 5.1.1. Documented evidence that a starting material supplier has a historical and ongoing technical capability of producing materials meeting this standard and who has proven, implemented procedures and capabilities in place to consistently produce acceptable product is a minimum requirement. Options for the technical approval of a starting material supplier include one or more of the following.API Spec 20B pdf download.API Spec 20B:2013 pdf free download
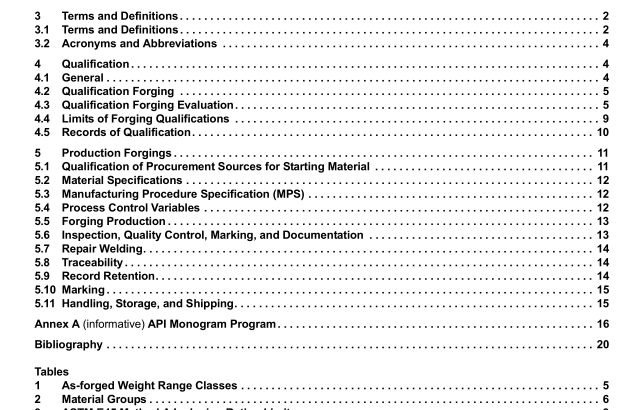