API Spec 12F:2008 pdf free download.Specification for Shop Welded Tanks for Storage of Production Liquids
5.15 Shell Attachment The tank deck shall be attached to the tank shell, if the deck if flanged, by a double-welded butt joint with complete penetration, or by a double-welded, full-fillet lap joint; or, if the deck is not flanged, by full-fillet welds, both inside and outside.
5.16 Cleanout Design Tanks shall be furnished with a 24-in. × 36-in. extended-neck cleanout, located as shown in Figure 1 and conforming to Figure 4. Cleanout cover plates shall be of one-piece construction, except that, if so specified on the purchase order they shall be of two-piece construction with a horizontal lap seam having one row of 1 / 2 -in. bolts on 2-in. centers with suitable gaskets and bolt retainers. If two-piece construction is specified, the top inspection plate shall have a clear opening of approximately 14 in. × 24 in., unless otherwise specified. When specified on the purchase order, handles for lifting the cleanout cover plate(s) shall be furnished.
5.17 Connections Design Tanks may be provided with inlet and outlet connections as shown in Table 1, Column 9 and Column 10, and Figure 1. Unless otherwise specified by the purchaser, connections shall be full couplings, and shall be attached to the tank member by full-fillet welds on both inside and outside surfaces, with equal projections inside and outside the tank, except that half couplings may be used for connections C-1, C-4, C-5, and C-6, at the option of the manufacturer. Additional or fewer connections of other sizes or locations may be provided, if so agreed between the purchaser and the manufacturer. When flanged or other types of connections are specified, the nozzle neck shall be a minimum of standard weight pipe and attached by full-fillet welds, both inside and outside. The bolting pattern for the thief hatch shall conform to Figure 1.
5.18 Anti-channel Drain Baffle Design An anti-channel drain baffle conforming to the following requirements shall be furnished if so specified on the purchase order.
a) The periphery of the baffle, in plan view, shall be 64 in.
b) The height of the baffle from the inside surface of the tank bottom to the top of the baffle shall be 4 in. minimum for 90-bbl tanks, and 5 1 / 4 in. minimum for all other sizes.
c) The baffle shall be equipped with spacers so that the bottom edge of the baffle is 1 in. above the tank bottom.
d) A drain line shall be provided from the baffle to the tank shell.
The line size shall be 3 in. nominal for 90-bbl tanks and 4 in. nominal for all other sizes.
e) The baffle shall be attached to the tank bottom by a J-bolt passing through an eye retainer welded to the tank bottom, and by the line connection to the tank shell. The baffle shall not be welded to the tank bottom.
5.19 Downcomer Pipe A downcomer pipe shall be installed if requested by the purchaser; design of downcomer to be by agreement between purchaser and manufacturer.
6 Venting Requirements
6.1 Normal Venting Connections C-1 and C-3 are provided for normal inbreathing and outbreathing due to temperature changes and to liquid movement into and out of the tank. These connections should be fitted with pressure-vacuum valves properly sized in accordance with API 2000. The pressure setting should be from 2 oz/in. 2 to 4 oz/in. 2 less than the opening pressure of devices used for emergency venting. Annex B is provided as a guide to aid in the selection of venting devices, where required.
6.2 Emergency Venting When storage tanks containing flammable liquids are exposed to fire, the venting rate may be in excess of that resulting from a combination of normal thermal effects and oil movement. Unless tanks are installed in remote locations, the purchaser shall provide, or cause to be provided, pressure relieving devices which will provide capacity in addition to normal venting to meet the requirements tabulated in Table C.1. API Spec 12F pdf download.API Spec 12F:2008 pdf free download
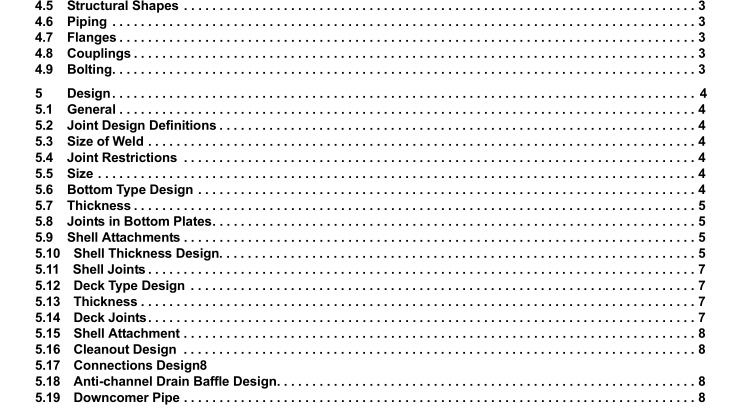