API TR 6MET:2010 pdf free download.Metallic Material Limits for Wellhead Equipment Used in High Temperature for API 6A and 17D Applications
n Phase I and II testing, three material test laboratories were selected to conduct elevated temperature tests in accordance with ASTM E21 using 0.505 in. diameter test specimens. One of the three laboratories with the best performance was selected to conduct all testing in Phase III. Phase I tensile specimens were removed from the mid- radius position. In Phase II and III tensile specimens were removed from the 1 / 4 T position where possible. Mechanical tests were then performed at room temperature (RT), 300 °F, 350 °F, and 450 °F to permit bracketing of results.
The Task Group analyzed the resulting yield strength (YS) data from all the labs for each heat of material. Finally each supplier’s data will be reported confidentially to that supplier only in exchange for the donation of material. The tensile properties at elevated temperature used conventional tensile testing equipment modified slightly to accommodate a radiant heating chamber. For precise control of temperature the chamber was well insulated which also minimized specimen exposure to undesirable surface contamination.
The heating chamber was monitored using two thermocouples to maintain precise temperature control. A single thermocouple was used to control chamber atmosphere temperature while the second thermocouple was attached to the test specimen.
Testing was initiated once the specimen and chamber atmosphere temperatures both reached equilibrium. Predetermined strain rates were maintained through break. Tensile strength determination was made by use of an attached Class B-2 extensometer.
The extensometer was modified to accommodate an extended reach into the heating chamber to fully engage the test piece through break while shielding the instrument from extreme temperatures. Full size round test specimens were utilized. Measurements to determine Percent Elongation and Percent Reduction of Area within the gage length were conducted on broken specimens after cooling sufficiently to facilitate handling. All test procedures and calibrations were in full compliance of ASTM E-21 without exception. No special equipment or processes were utilized in conducting hot tensile testing and there were no deviations to standard testing practices.
3 Results
3.1 Phase I Results Each material type was analyzed by comparing Yield Strength readings at RT, 300 °F, 350 °F, and 450 °F for each heat and laboratory individually using a pivot table. In this manner, differences due to material behavior and/or laboratory abnormalities could be easily detected.
Since the data set was too small to afford any statistical analysis, the results were averaged. Room temperature yield strength test results from three of the five heats of AISI 4130 were below 75 ksi. One heat was only 2 % below the required RT properties. However two of those three heats were 12 % and 17 % below the minimum requirement. Material certification reports were reviewed by metallurgists on the Task Group and reasons for the low properties were not obvious.
Averaging data from all the heats produced higher yield derating factors than seemed appropriate [92 % at 350 °F compared with current values in API 6A, for Carbon and Low Alloy steels of 85 % (see Bibliography)]. Consequently, results from two lowest property heats were ignored in the average, resulting in a yield derating of 90 % at 350 °F. This discrepancy from reported RT yield properties was not found on any of the other five alloys tested. The conclusion from this discovery is that low hardenability alloys used for heavy section equipment must have proper design qualification.
Thus averaging only three heats of 4130 produced an improved correlation to the other low alloy steel’s yield reduction ratio than averaging all five heats (see Annex A). One data point for 2 1 / 4 Cr 1 Mo at 450 °F appeared bad so it was excluded from the average. In all other cases, all data points for all five heats of the material were used.
The variation of results for heats within a material showed approximately 15 % over each temperature ranges, except for 410 which ran approximately 20 %. The variation between labs was approximately 10 % for most materials with one lab measuring on the low side in a majority of cases. A sample plot of average YS reduction ratio (derating factor) for 8630 is shown in Figure 1. Thus the derating factor at 400 °F was interpolated as 88.5 %.API TR 6MET pdf download.API TR 6MET:2010 pdf free download
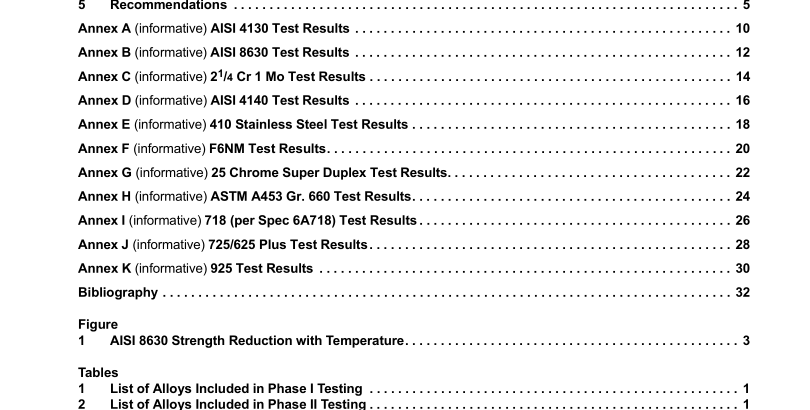