API RP 6HT:2013 pdf free download.Heat Treatment and Testing of Carbon and Low Alloy Steel Large Cross Section and Critical Section Components
4 Purpose Heat treatment is a critical process that must be appropriate and controlled in order to produce parts that comply with design requirements. Per API 6A, “The properties exhibited by the QTCs shall represent the properties of the thermal response of the material comprising the production parts it qualifies. Depending upon the hardenability of a given material, the QTC results might not always correspond to the properties of the actual components at all locations throughout their cross section.” The specified mechanical properties may not necessarily be required or achieved through the entire section thickness of the production part(s).
These procedures are intended to provide the manufacturer and end user with a means of ensuring that the qualification test coupon (QTC) is more representative of the mechanical properties in a large cross section component than can be expected with a standard API equipment specification QTC. Furthermore, these procedures are intended to provide to optimize the heat treatment and heat treatment response of large cross section components, thereby insuring that the component has the required mechanical properties at the depth below the surface established by the manufacture at all critical locations. It should be noted that the required mechanical properties as established by the manufacturer may be different from the mechanical properties required by the API equipment specification. This recommended practice is intended to supplement the heat treatment and testing requirements found in the API equipment specification and not to replace them altogether.
5 Application This recommended practice is intended for use on large cross section components being manufactured for conformance to API equipment specifications.
6 Recommended Heat Treating Practices
6.1 General Heat treating may be defined as the controlled heating and cooling of a metal in order to obtain a desired microstructure and consequently desired properties. Carbon and low alloy steels are the most widely used alloys in oil and gas exploration and production. One of the reasons for this is their versatility: a wide range of properties can be obtained through an appropriate heat treatment.
The basis for heat treating carbon and low alloy steels is that they have several different stable crystal structures depending on the heat treatment process used. By transforming the crystal structures during heat treatment, the desired microstructure and mechanical properties can be obtained in the end product, provided the size of the product does not exceed the hardenability limits of the alloy. The most common type of heat treatment imposed on carbon and low alloy steels is a three- to four-step process consisting of austenitizing, quenching, and tempering (Q&T) or normalizing, austenitizing, quenching, and tempering (N-Q&T).
The austenitizing cycle consists of heating the steel up to a temperature high enough to completely transform its microstructure into austenite (typically about 1 500 °F to 1 700 °F or 81 6 °C to 927 °C for most common low alloy steels). Austenite is a phase of steel having a face-centered cubic structure. The quenching cycle consists of removing the steel from the furnace and rapidly cooling it in a suitable liquid quench medium such as water, polymer, or oil before the temperature of any section of the component falls below the upper critical temperature. Ideally, the austenite transforms into a structure known as martensite during the quench and greatly harden the steel. Martensite generally has high strength but very low ductility, toughness, and resistance to brittle fracture. Austenite transforms into martensite only if a certain critical cooling rate is achieved. Slower rates result in other softer transformation products such as bainite, pearlite, and ferrite (in descending order of hardness). The actual cooling rate required to produce martensite is dependent on the alloying content of the steel.API RP 6HT pdf download.API RP 6HT:2013 pdf free download
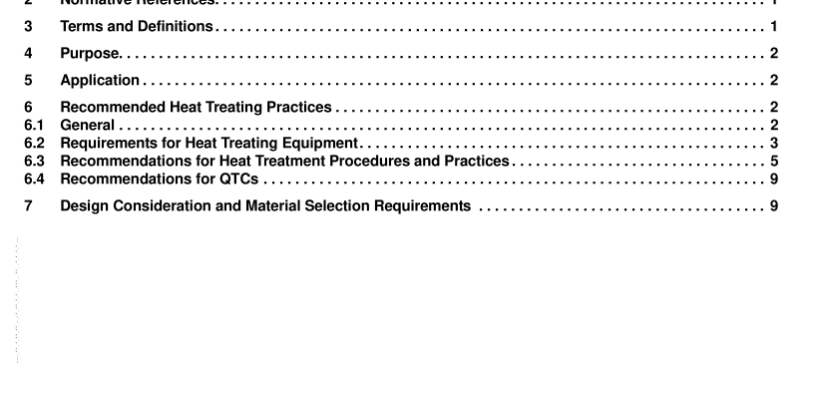