API St 609-2021 pdf free download.Butterfy Valves: Double-fanged, Lug- and Wafer-type, and Butt-welding Ends|
4.4 Diferential Pressure Rating
Diferential pressure rating shall not exceed the seat pressure rating.
5 Design
5.1 General
5.1.1 Category B Valves
Valves manufactured in accordance with this standard shall meet the requirements of ASME B16.34 for Standard class and any additional requirements as specifed in this standard. For materials not listed in ASME B16.34, the applicable requirements and design rules of ASME B16.34 shall be used. In the event of a confict between ASME B16.34 and this standard, this standard shall prevail.
5.1.2 Fire-tested Valves If the purchaser specifes fre-tested valves, the valve’s design shall have been type tested and certifed to meet all performance requirements of API 607. Fire test report shall be made available to purchaser upon request.
5.1.3 Fugitive Emissions Tested Valves If the purchaser specifes fugitive emission valves, the valve’s design shall have been type tested and certifed to meet all performance requirements of API 641. Fugitive emission test report shall be made available to purchaser upon request.
5.1.4 Cryogenic Service Valves required to operate in cryogenic service shall meet the additional requirements specifed in ANSI/MSS SP-134.
5.1.5 Lockable Device When specifed in the purchase order, valves shall be furnished with a lockable device that accepts a purchaser supplied lock that enables the valve to be locked in both the open and closed positions. The lockable device shall be designed such that a lock with an 8 mm ( 5 /16 in.) diameter shank, not more than 100 mm (4 in.) long, can be inserted directly through appropriate holes and locked. Provisions for a lockable device are permitted even when it is not specifed in the purchase order.
5.1.6 Disc Position Indication The indication of the position of the disc shall be integral with the valve shaft and shall be aligned with the valve disc. The indication may be accomplished by a mark on the shaft or by a shaft shape. The design shall ensure that a valve (and/or operator) cannot be assembled to falsely indicate the valve’s open and closed positions.
5.1.7 Shaft-to-lever Connections Shaft-to-lever connections shall be designed so that the lever always correctly indicates the disc position. The lever-type handle shall be mounted so that the handle is in parallel with the valve disc.
5.1.8 Category B Valves
a) Bidirectional—Category B valves: Bidirectional valves shall have a pressure rating of equal value in both directions. The pressure rating shall be marked in accordance with 8.1.
b) Preferred Direction—Category B valves: When specifed by the purchaser, the valve may have preferred and nonpreferred sealing direction. The pressure ratings of both the preferred and nonpreferred sealing directions shall be marked in accordance with 8.1.
5.1.9 Dead-end Service All components of lug-type and double-fanged valves designated for dead-end service by the purchaser (see B.1.3.f) shall pass the API 598 high-pressure closure test at 110 % of the valve’s diferential pressure rating in each direction. When the seat retainer is on the downstream side, the high-pressure closure test shall be performed with the seat retainer fully unrestrained (i.e. no downstream fange). Valves designed for dead-end service in only one installation direction require additional marking per 8.3.
5.2 Body
5.2.1 The minimum body-wall thickness shall comply with the applicable ASME B16 standard listed in Section 2 based on the body material. If the applicable standard covers fttings for a particular material, the valve minimum wall thickness shall be as specifed for fttings.
The valve design shall be structurally suitable for its stated pressure and temperature limits, taking into account that localized thinning may be necessary between the shaft bore in the body and the adjacent bolt holes. Such sections shall be designed in accordance with the requirements of ASME B16.34.
5.2.2 When a wafer-type valve is installed between piping fanges and the disc is in the closed position, the valve shall be self-centering to the fange bolting pattern, that is, designed to center itself within the bolt circle. Self- centering may be achieved by using the valve’s outside diameter or by means of integral or attached alignment devices.
5.2.3 End fanges for double-fanged valves shall be integrally cast or forged with the body; however, fanges may be attached by full-penetration butt-welding if agreed to by the purchaser. End fanges attached by welding shall conform to ASME B16.5 or ASME B16.47 as applicable and have butt-welding ends for use without backing rings. Welds shall conform to ASME B31.3, as shall qualifcations for the welding procedure and the welder or welding operator. The fnished weld thickness shall not be less than the minimum body-wall thickness. 5.2.4 Butt-welding ends shall conform to the requirements of ASME B16.25 with an inside diameter (denoted as “B” in ASME B16.25) tolerance per ASME B16.34.
5.2.5 If drain or bypass connections are specifed by the purchaser, they shall conform to ASME B16.34 or MSS SP-45, as applicable.API St 609 pdf download.API St 609:2021 pdf free download
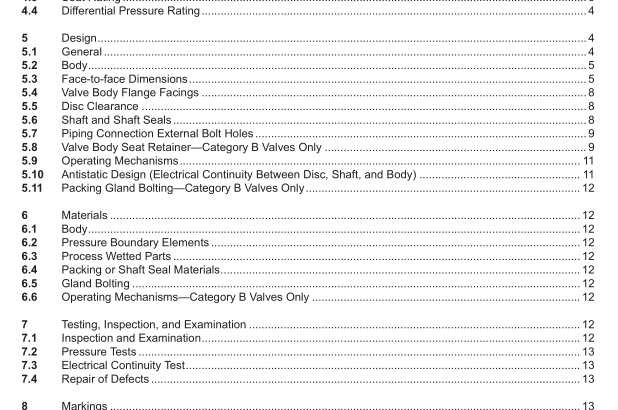