API RP 934-C:2019 pdf free download.Materials and Fabrication of 1 1 / 4 Cr- 1 / 2 Mo Steel Heavy Wall Pressure Vessels for High-pressure Hydrogen Service Operating at or Below 825 °F (440 °C)
6.1.3 Welding electrodes and fluxes shall produce low hydrogen weld deposits with a maximum of 0.27 fl oz (8 ml) of diffusible hydrogen for every 3.5 oz (100 g) of weld metal, per AWS A4.3. (These acceptable consumables are often designated with suffixes of H4 or H8). They shall be baked, stored, and used in accordance with the consumable manufacturer’s instructions (holding in electrode oven, length of time out of oven, etc.).
6.2 Mechanical Requirements
6.2.1 Tensile Properties The tensile properties of the deposited weld metal shall meet those of the base metal in accordance with 5.5.2.
6.2.2 Impact Properties Prior to the start of fabrication, each lot of electrodes, heat of filler wire, and combination of batch of flux and heat of wire, shall be impact tested and shall meet the requirements of 5.5.3. Welding, Heat Treatment, and Production Testing
7.1 General Welding Requirements
7.1.1 Base metal surfaces prior to welding or applying weld overlay shall consist of clean metal, prepared by machining, grinding, or blast cleaning.
7.1.2 Welded joints, including non-pressure attachments to the vessel body shall:
a) be full penetration joints. With approval by purchaser, this can be waived for external attachment welds, but any pockets which are formed shall be vented;
b) be located so that full ultrasonic examination of welds can be made after fabrication and after the equipment has been in-service. In cases where this is not practical, the manufacturer should propose alternate NDE methods to verify weld quality for the purchaser’s approval;
c) be made sufficiently smooth to facilitate NDE (MT, PT, UT, or RT), as applicable.
7.1.3 All welding shall be completed prior to final PWHT except welding of attachments to the internal corrosion resistant weld overlay or cladding, or to external stainless steel weld buildups, when permitted by the purchaser. For these attachment welds, a PQR or mockup test, or both, shall be performed to verify that this does not produce a HAZ in the base metal, unless waived by the purchaser.
7.1.4 Weld repairs to base metal, weld joints, and weld overlay shall be performed using a repair welding procedure qualified in accordance with 7.2 and shall meet all the same requirements as the normal fabrication welds.
7.1.5 No pressure-retaining dissimilar metal welds of ferritic to austenitic alloys shall be allowed, especially at stress riser sites such as the nozzle-to-shell, nozzle-to-head or nozzle-to-flange welds, except if allowed on a case-by-case basis by the purchaser. Dissimilar metal welds should also be avoided at nozzle to pipe connections with constraint mismatch and at thickness transitions. In some cases, purchasers have allowed dissimilar metal welds in the outle nozzles (typically in pipe-to-pipe or pipe-to-elbow welds) which extend to outside the skirts (with the weld typically located outside of the skirt).
There are cases where a dissimilar metal pipe-to-pipe weld is preferred over dissimilar metal flanges, depending on the process temperature and line sizes.
7.2 Welding Procedure Qualification Welding procedures shall be qualified in accordance with ASME Section IX, with the following additional requirements.
7.2.1 Base metal for welding procedure qualification tests shall be made from the same ASME base metal specification (same P-number and Group number) and similar in chemistry as specified for the vessel, but either plate or forging may be used. The welding consumable combination used (electrodes, wire and flux, whichever ones are applicable) shall be of the same type and brand as those to be used in production welding.
7.2.2 Vickers hardness traverses of the weld joint shall be made on a weld sample in the minimum PWHT condition. These hardness traverses shall be performed at locations similar to those shown in Figure 1. The HAZ readings shall include locations as close as possible [approximately 8 mils (0.2 mm)] to the weld fusion line. If previously-qualified WPS/PQRs are proposed, the purchaser shall decide if the hardness test locations are sufficient. For other weld geometries, refer to NACE MR 0103. The hardness shall not exceed 235 HV10.API RP 934-C pdf download.API RP 934-C:2019 pdf free download
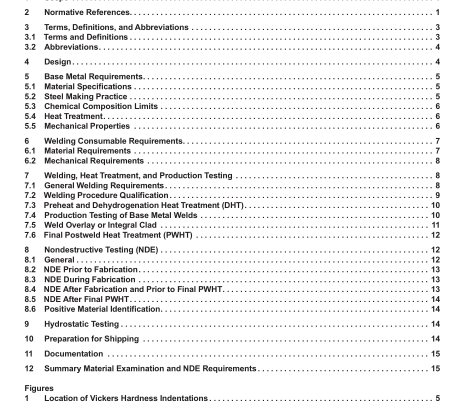