API 5LCP:2020 pdf free download.Specification for Coiled Line Pipe
7.5 LENGTH The length of pipe(s) shall be as specified on the purchase order. Agreement on overage and underage shall be agreed upon between the manufacturer and the purchaser, and specified on the purchase order. The accuracy of length measuring devices shall be ±1%.
7.6 PIPE-TO-PIPE WELDS By written agreement, and when specified on the purchase order, two or more lengths of pipe may be welded together by the man- ufacturer. See Appendix B. Weld surface hardness values shall not exceed those of Table 2.
7.7 WORKMANSHIP AND DEFECTS Imperfections of the types described in 7.7.1 – 7.7.10 that exceed the specified criteria shall be considered defects. The manufac- turer shall take all reasonable precautions to minimize recurring imperfections, damage, and defects.
7.7.1 Dents The pipe shall contain no dents greater than the specified wall thickness, measured at the gap between the lowest point in the dent and a prolongation of the original contour of the pipe. The length of the dent in any direction shall not exceed one half of the diameter of the pipe. All cold-formed dents deeper than 1 / 8 -in. (3.2-mm) with a sharp bottom gouge shall be considered a defect. The gouge may be removed by grinding.
7.7.2 Offset Skelp Edges The radial offset of the skelp edges of the longitudinal weld shall not exceed 0.020 in. (0.5 mm) or 0.1t, whichever is greater.
7.7.3 Height of Outside Flash The outside flash shall be trimmed to an essentially flush condition.
7.7.4 Height of Inside Flash Where, by agreement between the purchaser and the manufacturer, the inside flash is not to be removed, the following require- ments apply: For pipe sizes less than 3 1 / 2 , the inside flash shall not extend above the prolongation of the original inside surface of the pipe more than 0.090 in. (2.3 mm), or the specified wall thickness, t, whichever is less. For pipe sizes 3 1 / 2 and above, the flash height shall not exceed 0.125 in. (3.2 mm) Otherwise, the inside flash shall be trimmed and shall not extend above the prolongation of the original inside surface of the pipe more than 0.020 in. (0.5 mm), or as agreed upon between the purchaser and the manufacturer.
The inside diameter at which internal flash can not be trimmed should be determined during contract review.
7.7.5 Cracks and Leaks All cracks and leaks shall be considered defects
. 7.7.6 Laminations and Inclusions Any lamination or inclusion extending into the face or bevel of the pipe and having a transverse dimension exceeding 1 / 4 in. (6.4 mm) is considered a defect. Pipe containing such defects shall be cut back until no lamination or inclusion is greater than 1 / 4 in. (6.4 mm). Any lamination in the body of the pipe greater than or equal to 3 / 8 in. (9.5 mm) in the minor dimension is considered a defect. Disposition of such defects shall be in accordance with 8.6.9, item a or b. No specific inspection for laminations or inclusions by the manufacturer is required unless the purchaser specifies special nondestructive inspection on the purchase order.
7.7.7 Arc Burns Arc burns are localized points of surface melting caused by arcing between electrode or ground and pipe surface, and shall be considered defects. Disposition of pipe containing arc burns shall be in accordance with 8.6.9 except that removal of defects by grinding shall be subject to the following additional conditioning: a. Arc burns may be removed by grinding, chipping, or machining.
The resulting cavity shall be thoroughly cleaned and checked for complete removal of damaged material by etching with a 10% solution of ammonium persulphate or a 5% solution of nital. b. If removal of damaged material is complete the cavity may be merged smoothly into the original contour of the pipe by grind- ing, provided the wall thickness is within specified limits.
7.7.8 Undercuts at Pipe-To-Pipe Welds Undercutting of pipe-to-pipe welds is the reduction of thickness of the pipe wall adjacent to the weld where it is fused to the sur- face of the pipe. Undercutting on the outside surface can best be identified and measured visually. (Undercutting on the inside sur- face can be identified using radiographic or ultrasonic means). Minor undercutting on either the inside or the outside of the pipe is defined as follows and is acceptable without repair or grinding: a. Maximum depth 1 / 32 in. (0.8 mm) and not exceeding 10% of the wall thickness with a maximum length of one-half the wall thickness and not more than two such undercuts in any 1 ft (0.3 m) of the weld length. b. Maximum depth of 1 / 64 in. (0.40 mm) any length. Undercutting in excess of Item (a) above shall be considered a defect. Disposition shall be as follows: a. Undercut defects not exceeding 1 / 32 in. (0.8 mm) in depth and not exceeding 10% of the specified wall thickness shall be removed by grinding in accordance with 8.6.6, Item a. b. Disposition of undercuts greater in depth than 1 / 32 in. (0.8 mm) or 10% of the specified wall thickness shall be in accordance with 8.6.9 Item b.
7.7.9 Pipe-to-Pipe Radial Offset For all pipe, the radial offset at pipe-to-pipe welds shall not exceed 0.020 in. (0.5 mm) or 0.1t, whichever is greater.API 5LCP:2020 pdf free download
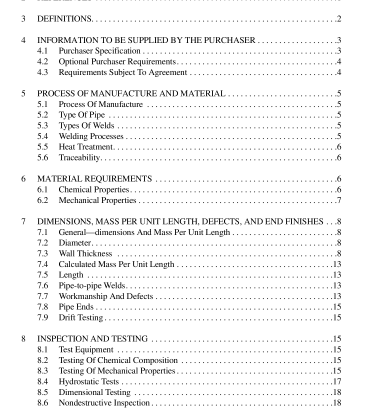