API RP 939-C:2009 pdf free download.Guidelines for Avoiding Sulfidation (Sulfidic) Corrosion Failures in Oil Refineries
4 Basics of Sulfidation Corrosion
Sulfidation corrosion, also often referred to as sulfidic corrosion, is not a new phenomenon, but was first observed in the late 1800s in a pipe still (crude separation) unit, due to the naturally occurring sulfur compounds found in crude oil. When heated for separation, the various fractions in the crude were found to contain sulfur compounds that corroded the steel equipment. With the advent of fluidized catalytic cracking (FCC) and coking processing, sulfidation corrosion was also experienced in these units [1], [2] . When hydroprocessing was introduced in the 1950s, changes in the corrosion behavior of construction materials were noted. This led to the recognition that a different sulfidation corrosion behavior resulted under hydroprocessing conditions which typically involve the presence of hydrogen.
Empirical industry data as well as laboratory research indicates that the sulfidation corrosion rate is a function of a variety of factors including: temperature, the total sulfur concentration, the types of sulfur compounds present, the type of stream (e.g. light gas or heavy oil), the velocity (or flow regime), heat transfer conditions, the presence or absence of hydrogen, and the material of construction.
In the absence of hydrogen, corrosion due to sulfur compounds in the crude typically is thought to occur at temperatures above 450 °F (230 °C). As discussed below, the industry relies on a set of curves (the modified McConomy curves [3] ) to predict corrosion rates. These curves show that at a given temperature and total sulfur level, steels with increasing chromium content (from carbon steel, to 5Cr to 9Cr to stainless steel) will experience lower corrosion rates. In the presence of hydrogen, i.e. H 2 /H 2 S corrosion, corrosion starts to increase above about 450 °F (230 °C). The industry relies on a set of curves (the Couper-Gorman curves [4] ) to predict the corrosion rate in this environment.
These curves relate the amount of H 2 S present with temperature to determine the corrosion rate. At a given H 2 S content and temperature, increasing Cr content of low to medium alloys makes little or no difference in corrosion rates. It is typically necessary to use 18Cr-8Ni stainless steels in order to achieve a significant improvement in corrosion resistance. Each crude oil or crude blend has its own unique characteristic chemistry, sulfur compounds, and effect on sulfidation corrosion.
Despite the industry’s best efforts, the accurate prediction of the resulting H 2 -free sulfidation corrosion rate for a specific crude oil and its fractions is an elusive technical challenge. Oil refineries that processed a consistent diet of a particular crude oil or crude blend could often base future predictions on past experience. However, over the past 20+ years, global economics have resulted in many refineries processing tens of different crudes in any given year; thus, minimizing the accuracy, or even feasibility, of predictions based on historical data. Additionally, the verification of the actual corrosion rate experienced while processing a specific crude oil is very difficult. Sulfidation corrosion results in wastage of the wall thickness of fittings, piping, heater tubes, and pressure vessels.
Most industry incidents have occurred in piping components, due to their thinner overall wall thicknesses and their higher population density vs the other equipment types. Although sulfidation corrosion under certain circumstances can be localized, the majority of sulfidation corrosion damage is general or uniform in nature, i.e. present over a fairly large surface area of a given component and not dependent on differenced between local conditions and bulk conditions. As a result when general thinning occurs, ruptures are possible leading to the potential release of large quantities of hydrocarbon streams. Figure 1 to Figure 4 show piping components that experienced H 2 -free sulfidation corrosion.
5 Location of Sulfidation
Corrosion Sulfidation corrosion can occur wherever sulfur compounds are present in a hydrocarbon stream and the temperature exceeds approximately 450 °F (230 °C). H 2 /H 2 S corrosion can also occur in the absence of hydrocarbon. API 571 contains generic process flow diagrams for typical refinery units and identifies where H 2 -free sulfidation corrosion and H 2 /H 2 S corrosion occurs. H 2 -free sulfidation most commonly occurs in the hotter areas of the following types of units: crude, vacuum, coker, visbreaker, and hydroprocessing feed and distillation sections. H 2 /H 2 S corrosion most commonly occurs in hydroprocessing units such as desulfurizers, hydrotreaters and hydrocrackers downstream of the hydrogen injection point through the reaction section to the separation section.API RP 939-C pdf download.API RP 939-C:2009 pdf free download
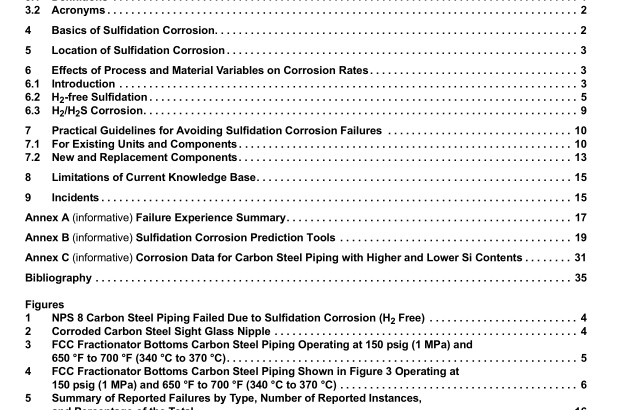